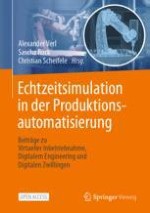
Open Access 2024 | OriginalPaper | Buchkapitel
21. Strukturmodellbasierte Korrektur thermisch bedingter Fehler
verfasst von : Steffen Ihlenfeldt, Xaver Thiem, Jens Müller
Erschienen in: Echtzeitsimulation in der Produktionsautomatisierung
Verlag: Springer Berlin Heidelberg
Aktivieren Sie unsere intelligente Suche, um passende Fachinhalte oder Patente zu finden.
Wählen Sie Textabschnitte aus um mit Künstlicher Intelligenz passenden Patente zu finden. powered by
Markieren Sie Textabschnitte, um KI-gestützt weitere passende Inhalte zu finden. powered by