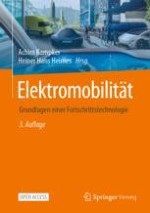
Open Access 2024 | OriginalPaper | Buchkapitel
19. Lösungsstrategien der Produktentstehung
verfasst von : Heiner Hans Heimes, Achim Kampker, Christian Offermanns, Konstantin Sasse, Jonas Gorsch, Kai Kreisköther, Ruben Förstmann, Carsten Nee
Erschienen in: Elektromobilität
Verlag: Springer Berlin Heidelberg
Aktivieren Sie unsere intelligente Suche, um passende Fachinhalte oder Patente zu finden.
Wählen Sie Textabschnitte aus um mit Künstlicher Intelligenz passenden Patente zu finden. powered by
Markieren Sie Textabschnitte, um KI-gestützt weitere passende Inhalte zu finden. powered by